Besides undertaking industrial projects in Mould Design, the section also provides design consultancy, EDM die-sinking and wire-cutting, and injection moulding services to support industrial development projects. We have three laboratories to support these training activities and industry projects.
Our Facilities
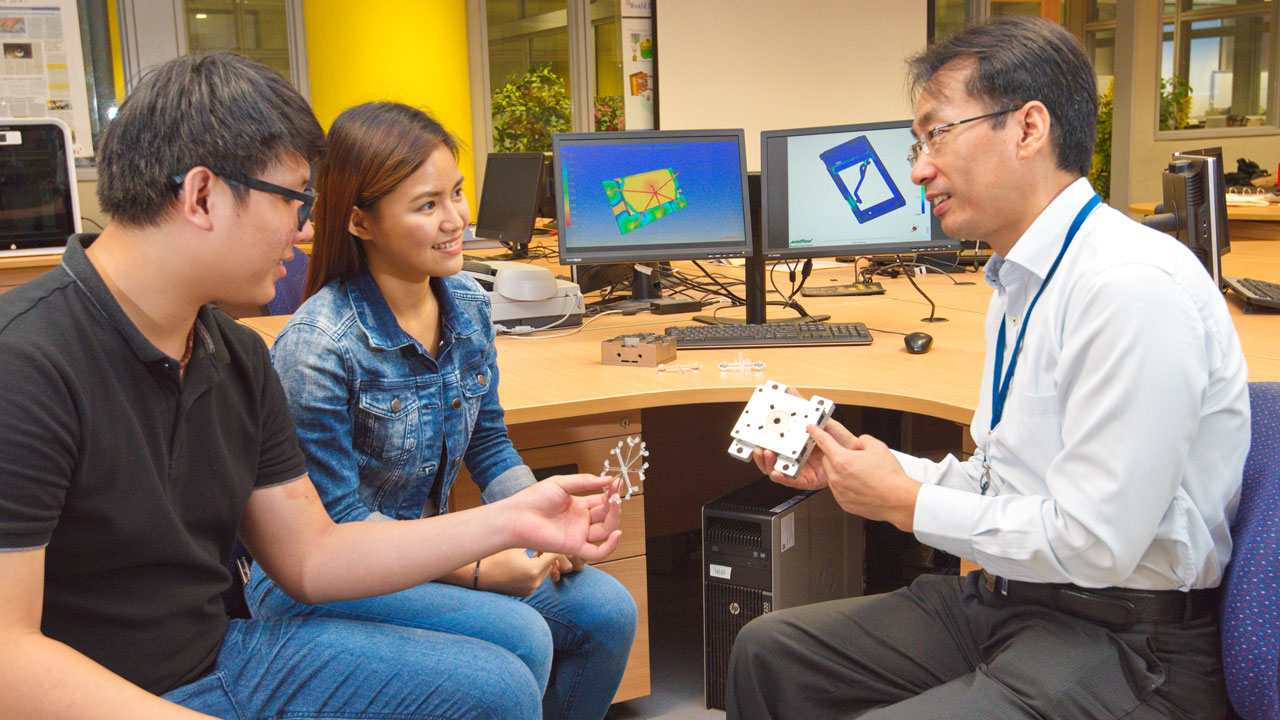
Digital Mould & Tool Design Lab
- Product Design and Development
- Mould Flow Simulation and Analysis
- Design of Injection Moulds
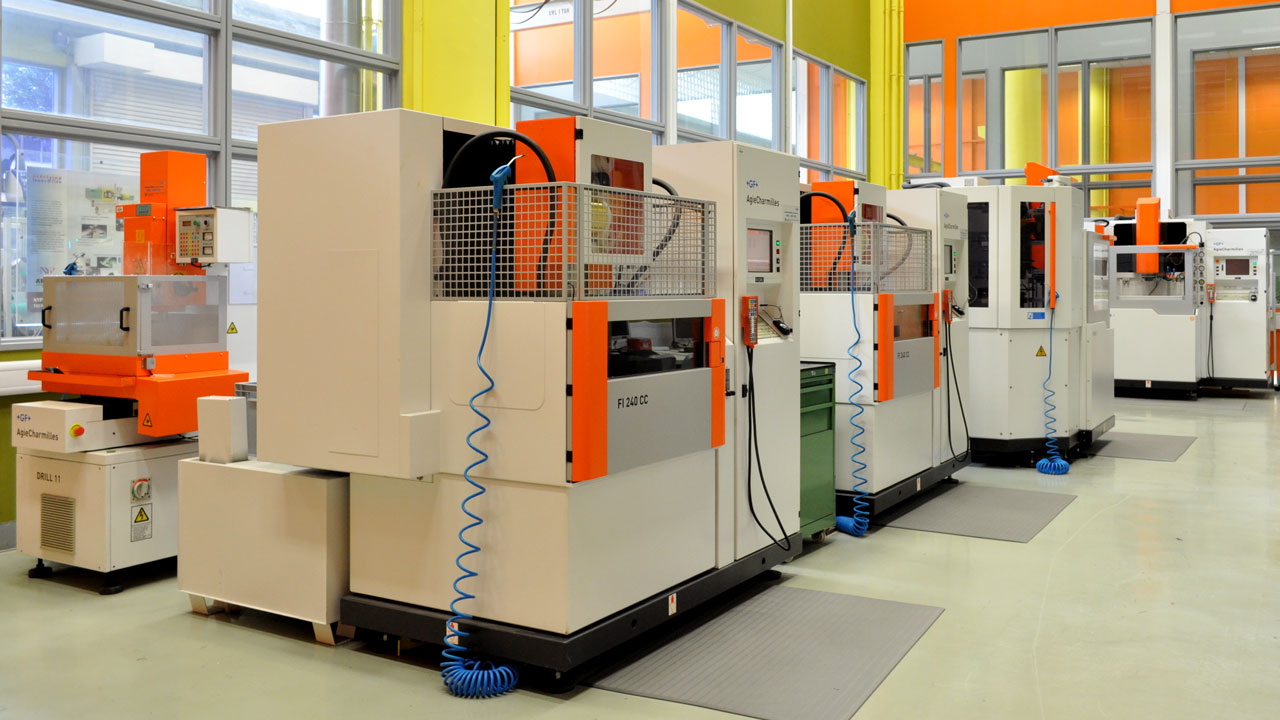
Integrated Toolroom & Plastics Technology Lab
- Electrical Discharge Machining (EDM) Die-Sinking & Wire-cutting
- Micro Moulding
- Lens Moulding
- LSR Moulding
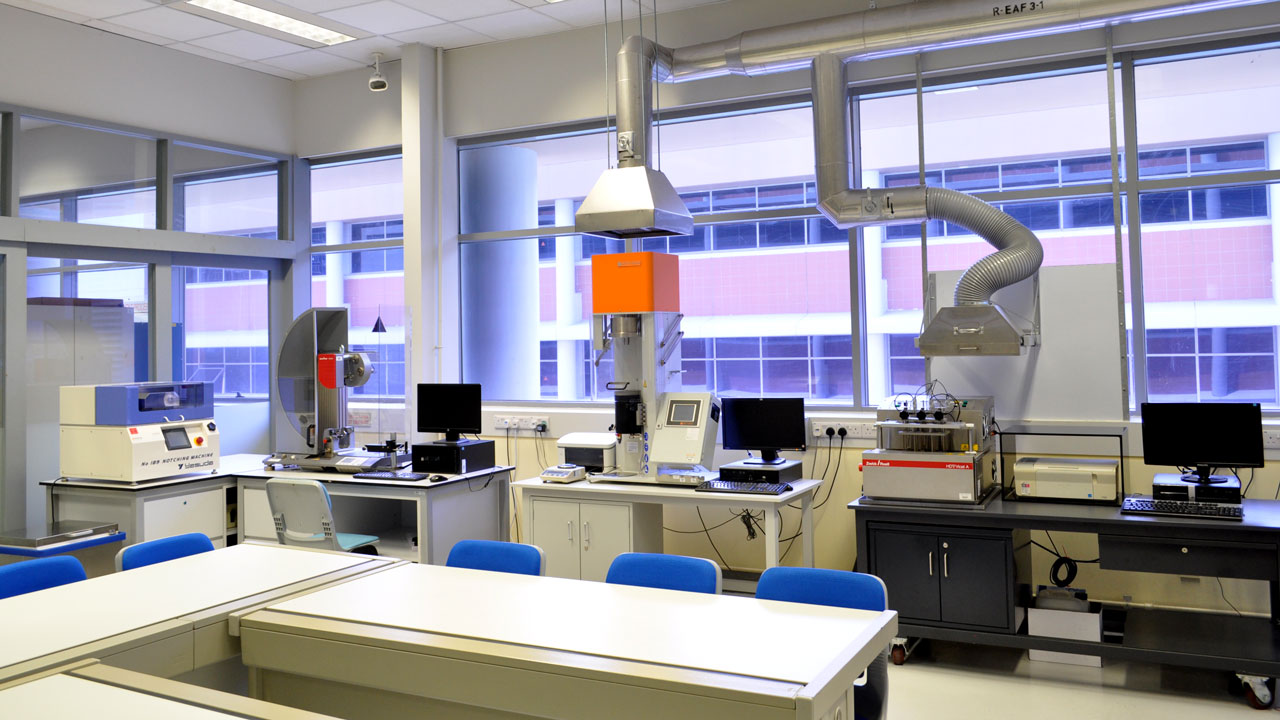
Plastics Materials Testing Lab
- Tensile Test for Polymer materials
- Melt Flow Index/Rate Testing (MFI/MFR)
- Impact Testing
- Heat Deflection Temperature/Vicat Softening Temperature Testing (HDT/Vicat)
- Differential Scanning Calorimeter Analysis (DSC)
Case Studies
Micro injection moulding process is a key enabling technology for micro manufacturing and is widely used as a cost-effective mass production method for a diversity of micro precision-moulded plastic components.
To meet the challenge in producing micro components with stringent requirements, innovative mould design concepts and systematic approach to moulding process have been adopted. Advanced machining technology has been employed to produce complex 3D micro tooling structures.
A two-cavity mould for producing micro components used in hearing aid. Under cut features are released using miniature pneumatic cylinders.
- Vacuum-assisted mould filling
- Precise mould temperature control
- Effective cavity venting
- Low-weight mould frame
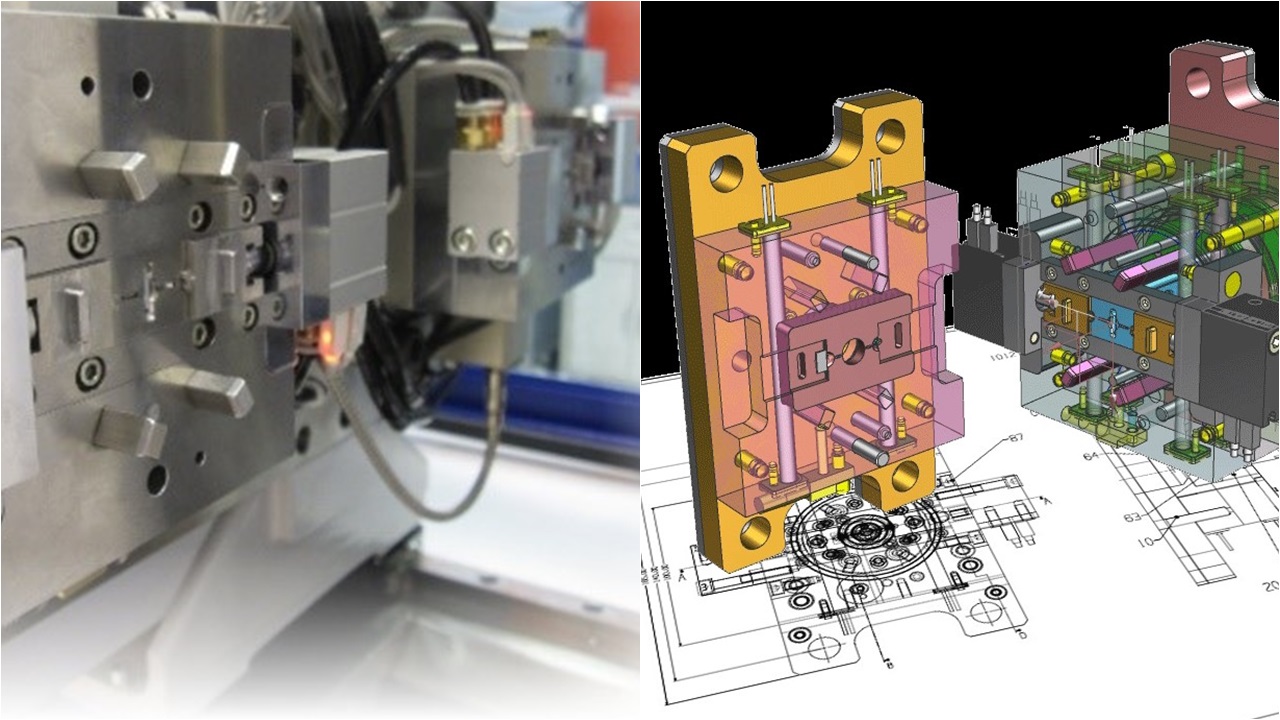
Contact us
- Mr Kent Loo
- Tel: 6550 0598
- Email: kent_loo@nyp.edu.sg