The Additive Manufacturing Innovation Centre (AMIC) supports companies in meeting the challenges of product design and development.
Our team of experienced and competent professional Senior Lecturers, Development Engineers and Development Technologist in various technological areas are well-prepared and dedicated to take on the challenge and needs of the industry.
Our Services
- Customised training programmes in Additive Manufacturing
- Consultation
- Product Design & Development
- Design for Additive Manufacturing
- Rapid Tooling, Hybrid Tooling & Conformal Cooling Technology
- Rapid Fixturing
- Full turnkey solutions
Our Capabilities
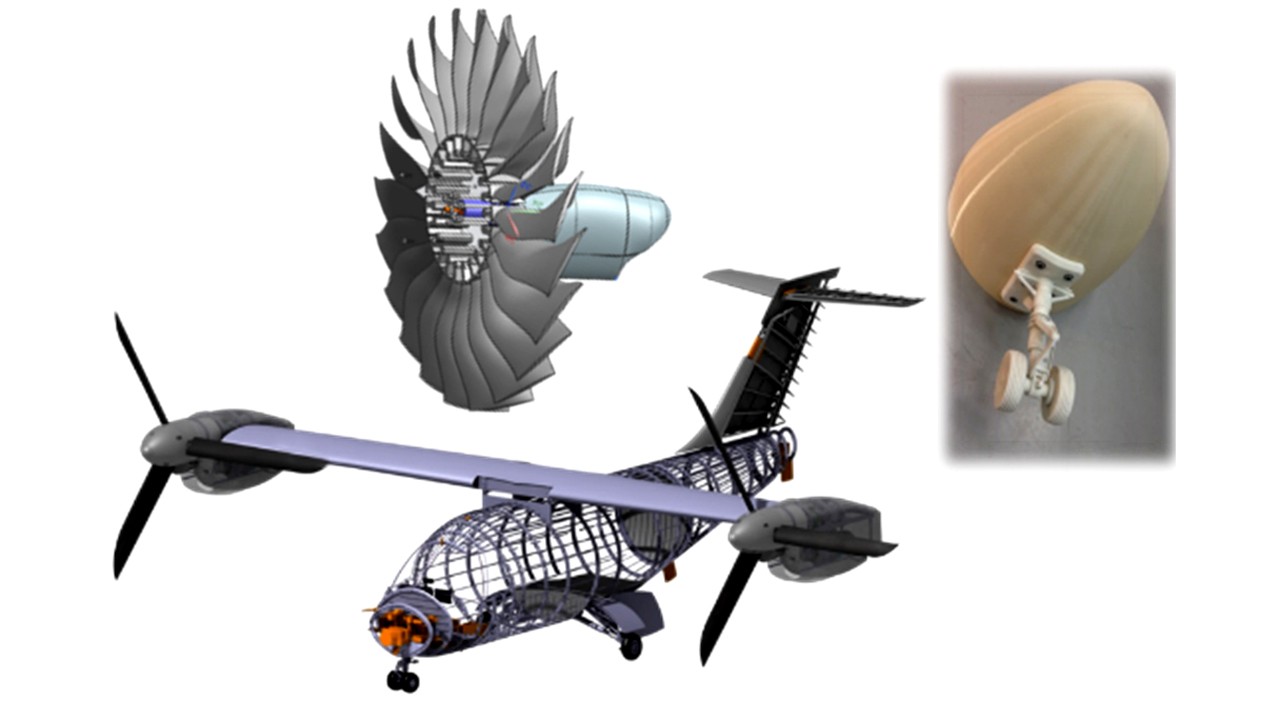
Innovative Product Design, Development and Industrial Design
3D Printing/Additive Manufacturing brings virtual designs to real life and changing our consumer market. It allows to customise the product design based on user preference. We have accumulated extensive experience working with industrial partners in consumer and medical product design, simulation, analysis and development. We are able to provide turnkey product development solutions.
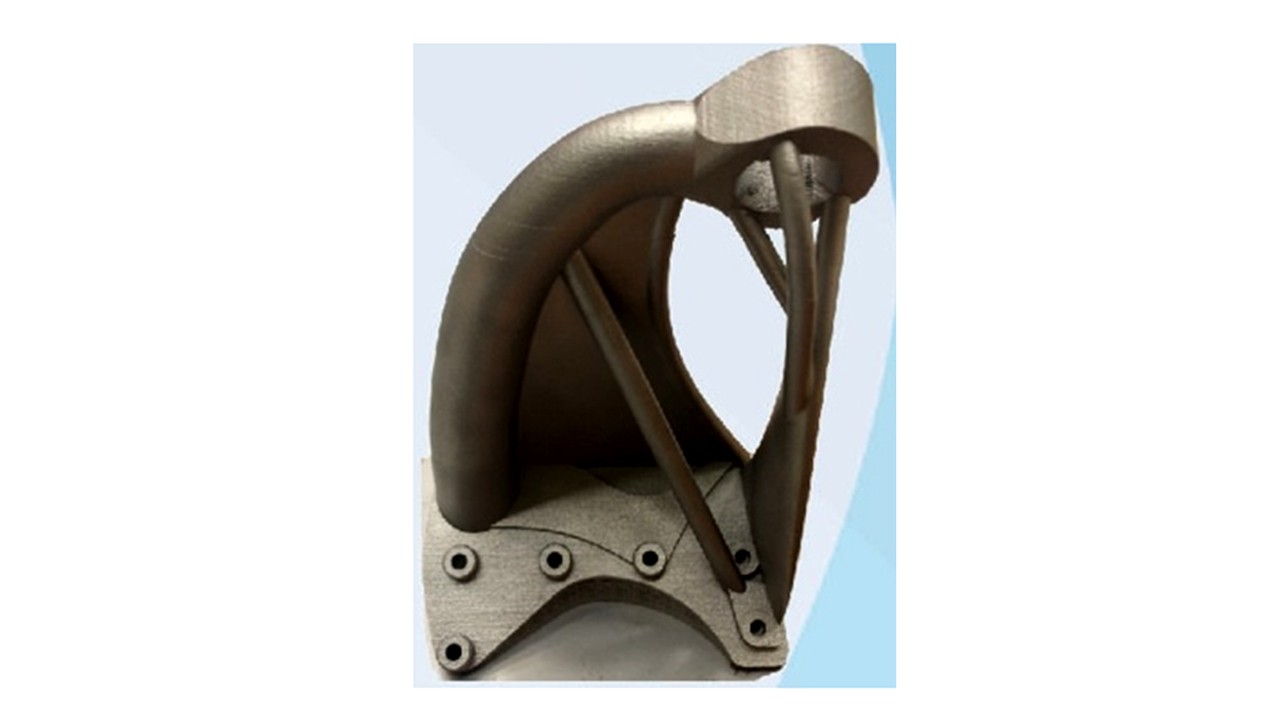
Design for Additve Manufacturing
We are able to optimise the products by light weighting, topology optimisation (biomimicry) and transforming lattice structures if required with considerations of fabrication process by 3D printing/Additive Manufacturing. It is used in aerospace, medical and robotic & automation components. It can also be applied in product redesign for functionality with reduction in number of assembly components.
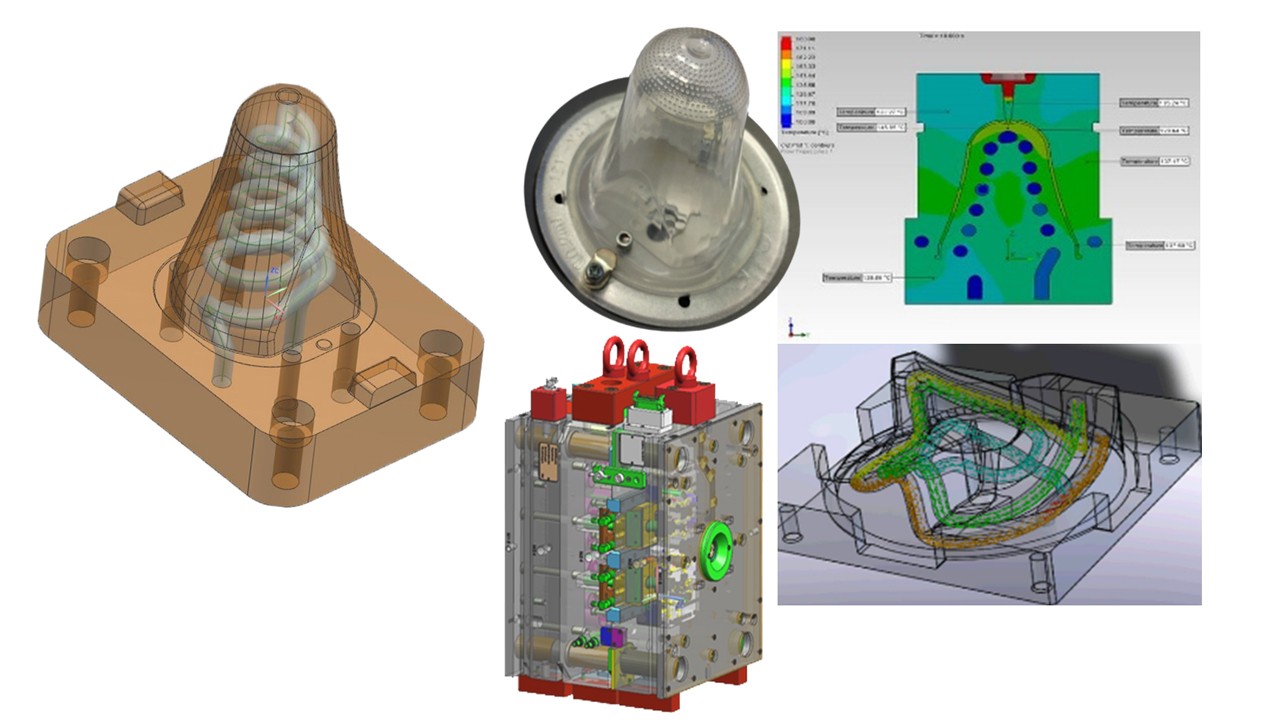
Rapid Tooling, Hybrid Tooling & Conformal Cooling
We have developed and fabricated several rapid tooling inserts for our industrial customer. The rapid tooling inserts are built using the Direct Metal Laser Melting process. Complex conformal cooling channels can be incorporated in the insert for improvement in product quality and shorter moulding cycle time.
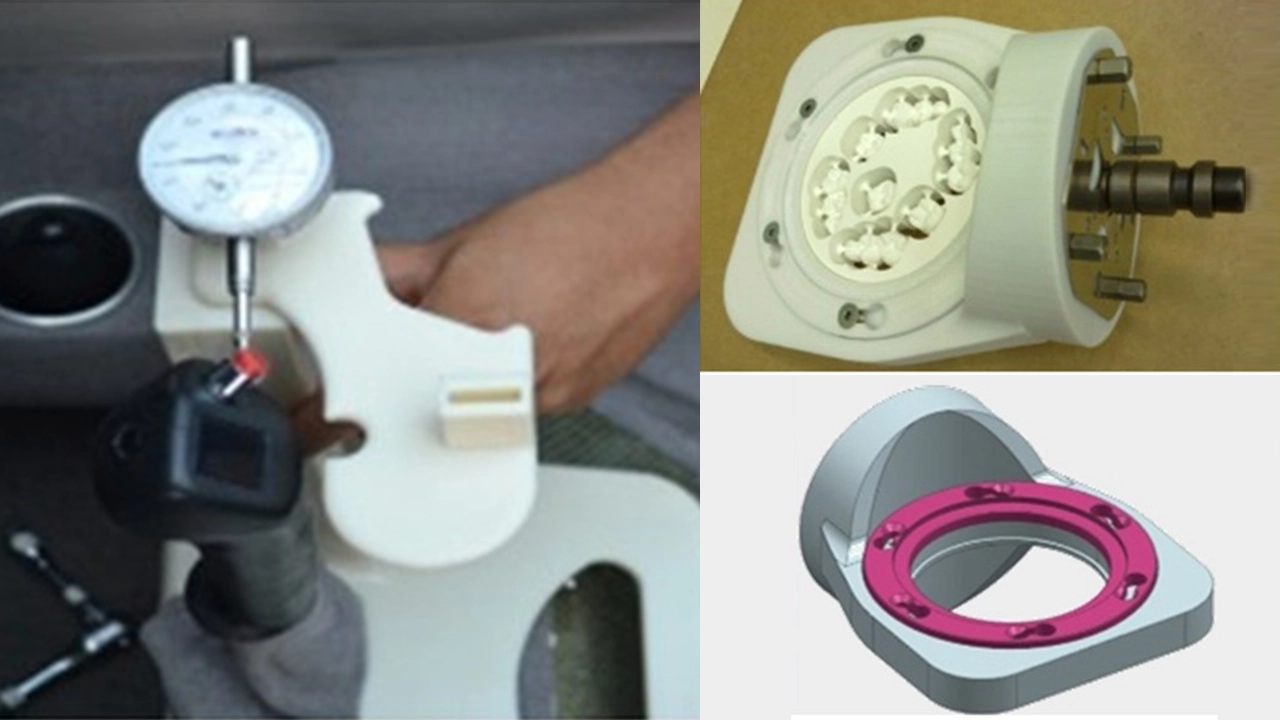
Rapid Fixturing
Fast and flexible fabrication of jigs & fixtures could be done using additive manufacturing techniques. Complex fixtures could be designed and fabricated in non-traditional way.
Unleash the Potential of Additive Manufacturing
Our Additive Manufacturing (AM) capabilities encompass a wide range of technologies, including:
- Rapid Prototyping: Quickly iterate and validate designs with functional prototypes.
- Functional AM: Produce end-use parts with the required mechanical properties.
- Multi-material AM: Combine materials within a single print for parts with varying stiffness, flexibility, or colour.
- Assembly Printing: Eliminate the need for separate components by printing functional assemblies.
For vibrant product development and production, our multi-colour multi-material technology allows you to create plastic parts with:
- Multiple Colours: Enhance aesthetics and branding with a wider colour palette.
- Varied Material Properties: Combine rigid and flexible regions within a single print for features like non-slip grips or living hinges.
- Simplified Assemblies: Reduce complexity by printing multi-functional parts, eliminating the need for separate components.
With Metal 3D Printing, we can unlock new frontiers in manufacturing together. By building complex objects layer-by-layer, this technology enables:
- Cost-Effective Production: Create intricate geometries that are difficult or expensive with traditional methods.
- Design Innovation: Unleash your design creativity with complex features and lattice structures.
Our Facilities
Our facilities include a spread of Additive Manufacturing Processes: Stereolithography (SLA),Selective Laser Sintering (SLS), Fused Deposition Modelling (FDM), Direct Metal Laser Sintering (DMLS),Selective Laser Melting (SLM) & Polyjet 3D Printing & Hybrid AM machines supported by its post processing equipment such as Vacuum Casting, Micro Peening, CNC Mill/Turn/EDM/Wi recut, Laser Scanner,CMM, CT and Material Testing Equipment etc.
Type of AM machines at AMIC
- Vat Photopolymerization: SLA Prox800
- Material Jetting: Objet 500 Connex3
- Powder Bed Fusion: HP5200, M290, Concept Laser M2, SLM280
- Material Extrusion (FDM): Fortus900, Fortus 450, F170, V-Shaper
- Plastic Material: PA, Nylon, PC, ABS, PC-ABS, Ultem, digital materials
- Metal Material: S.S, Maraging Steel, Starvax, Cobalt Chrome, Ti, Al, Inconel, Copper
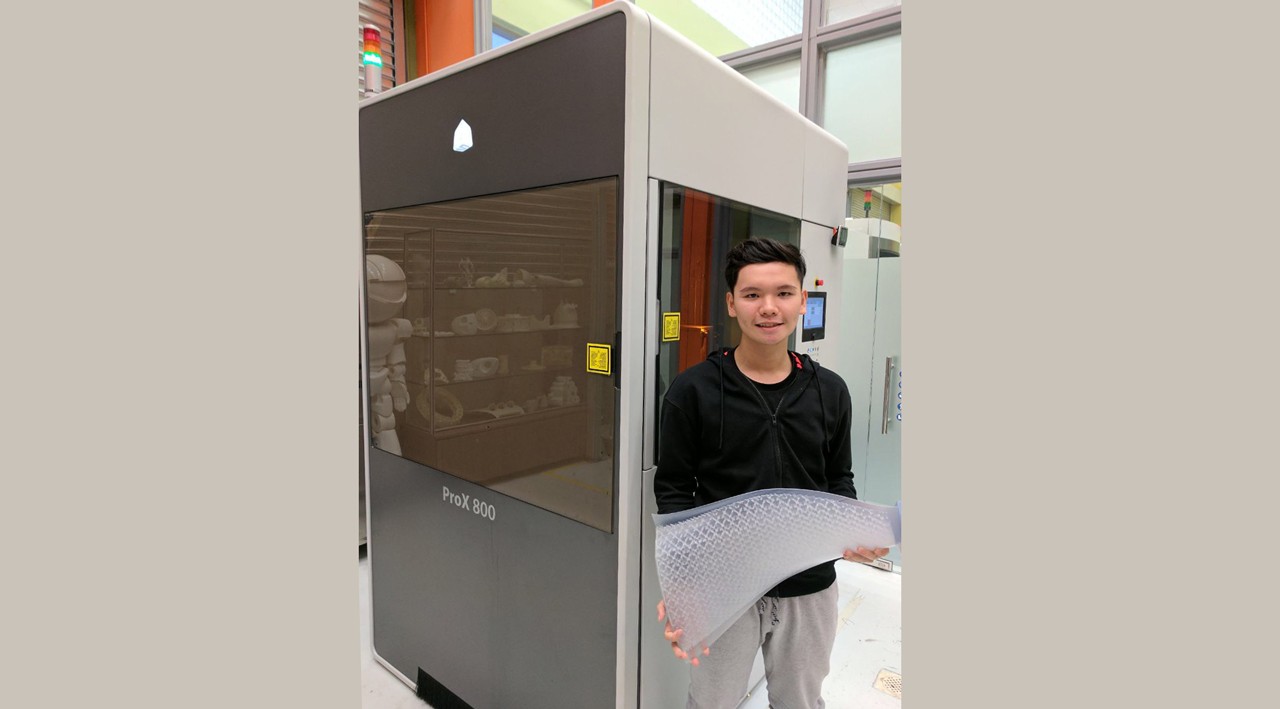
Stereolithography Apparatus (SLA) Process SLA ProX 800
Process:
Scanning of UV laser beam over the cross section of the model in liquid resin and building up layer by layer.
Material Used:
Accura 60(PC Similar)
Maximum Build size :
650mm x 750mm x 550mm
Application :
- Concept modeling
- Form fit, assembly tests
- Master pattern for vacuum casting
- Models for stress optical checking
- Other applications
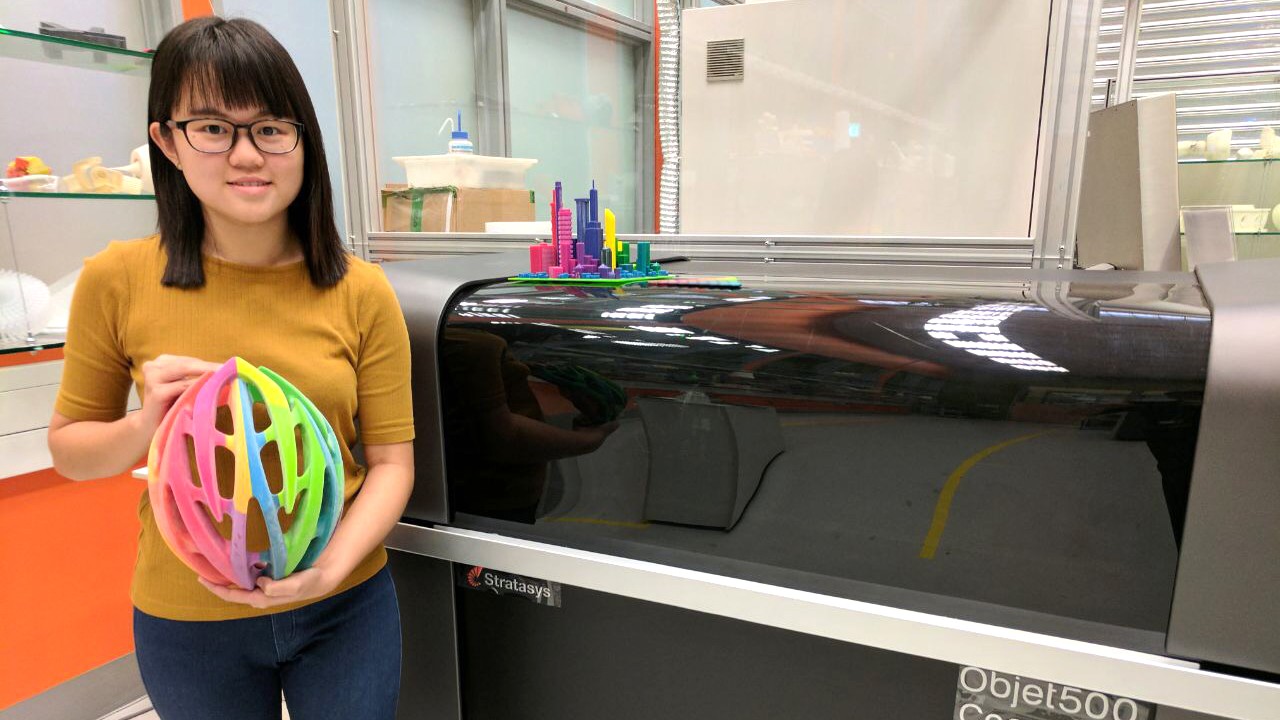
Material Jetting Process Objet 500 Connex 3
Process:
Inkjet print heads are used to deposit materials on demand onto a build platform. The material solidifies which allows to build layers on top of each other.
Material Used:
Clear, rubberlike photopolymers, and tough high-performance thermoplastics. Able to combine many colors and material properties into one model.
Maximum Build size :
490mm x 390mm x 200mm
Application :
- Concept modeling
- Form fit, assembly tests
- Functional Prototypes
- Transparent and rubber like model
- Other applications
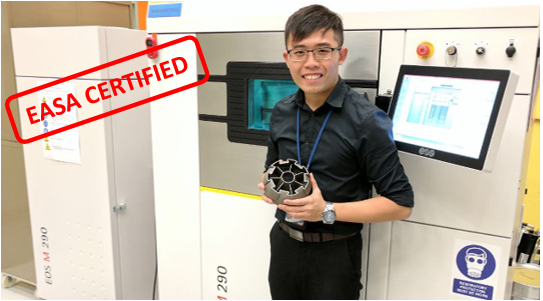
Direct Metal Laser Melting Processes EOSINT 290
European Union Aviation Safety Agency (EASA) Certified
Process
Scanning of laser beam over the cross section of the model in the metal powder and building up layer by layer.
Material used:
Stainless Steel, Maraging Steel (MS1), Aluminium (AlSi10Mg), Titanium (Ti64), Inconel 718
Maximum Build Size:
250mm x 250mm x 325mm
Application:
- Rapid Tooling Insert with Conformal Cooling
- Metal components
- Hybrid prototypes
- Other applications
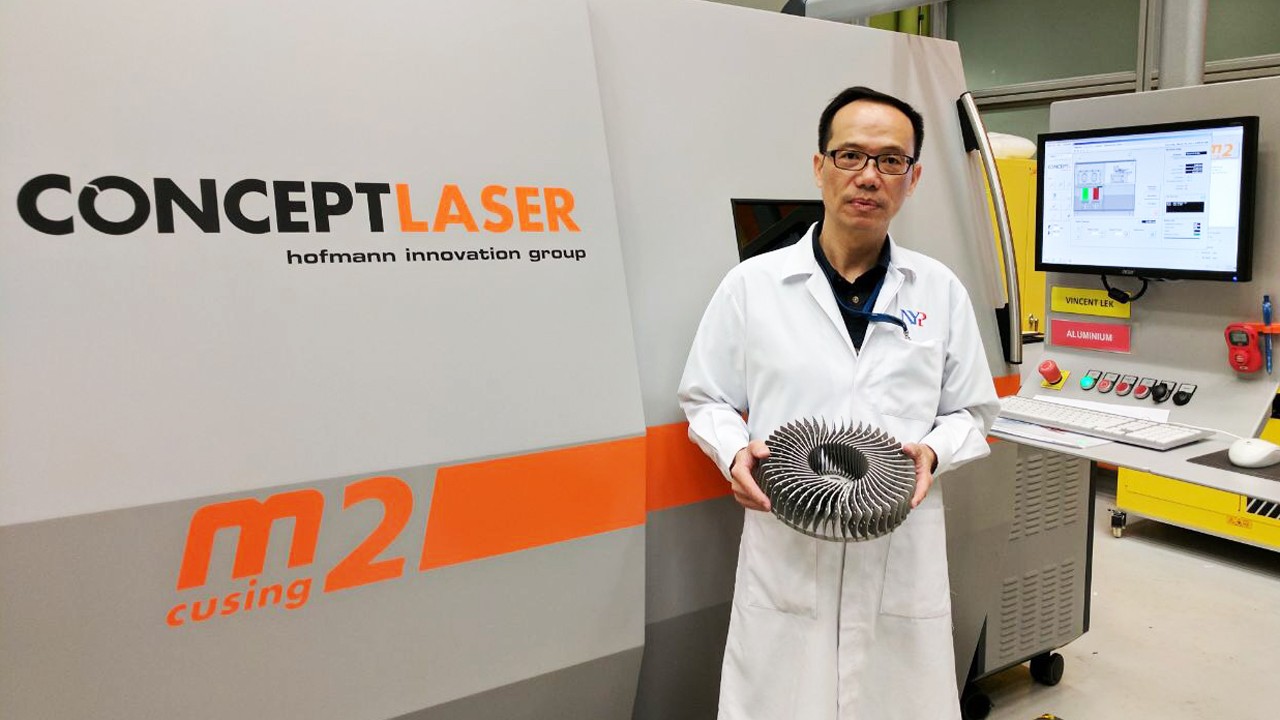
Concept Laser M2
Process
Scanning of laser beam over the cross section of the model in the metal powder and building up layer by layer.
Material used:
Stainless Steel, Maraging Steel (MS1), Aluminium (AlSi10Mg), Titanium (Ti64)
Maximum Build Size:
250mm x 250mm x 280mm
Application:
- Rapid Tooling Insert with Conformal Cooling
- Metal components
- Hybrid prototypes
- Other applications
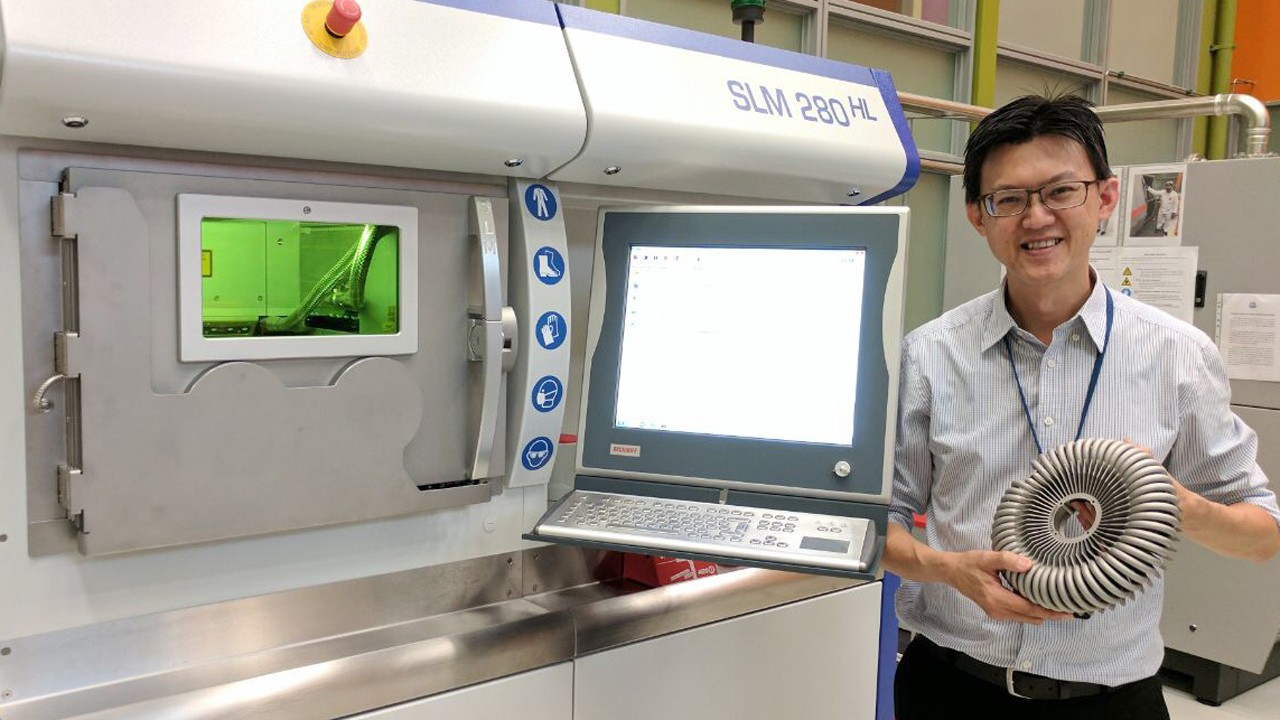
SLM 280 (under American Bureau of Shipping (ABS) Certification)
Process
Scanning of laser beam over the cross section of the model in the metal powder and building up layer by layer.
Material used:
Stainless Steel 316L, Maraging Steel (MS1), Aluminium (AlSi10Mg), Titanium (Ti64)
Maximum Build Size:
280mm x 280mm x 365mm
Application:
- Metal components
- Hybrid prototypes
- Aerospace, automotive and marine
- Other applications
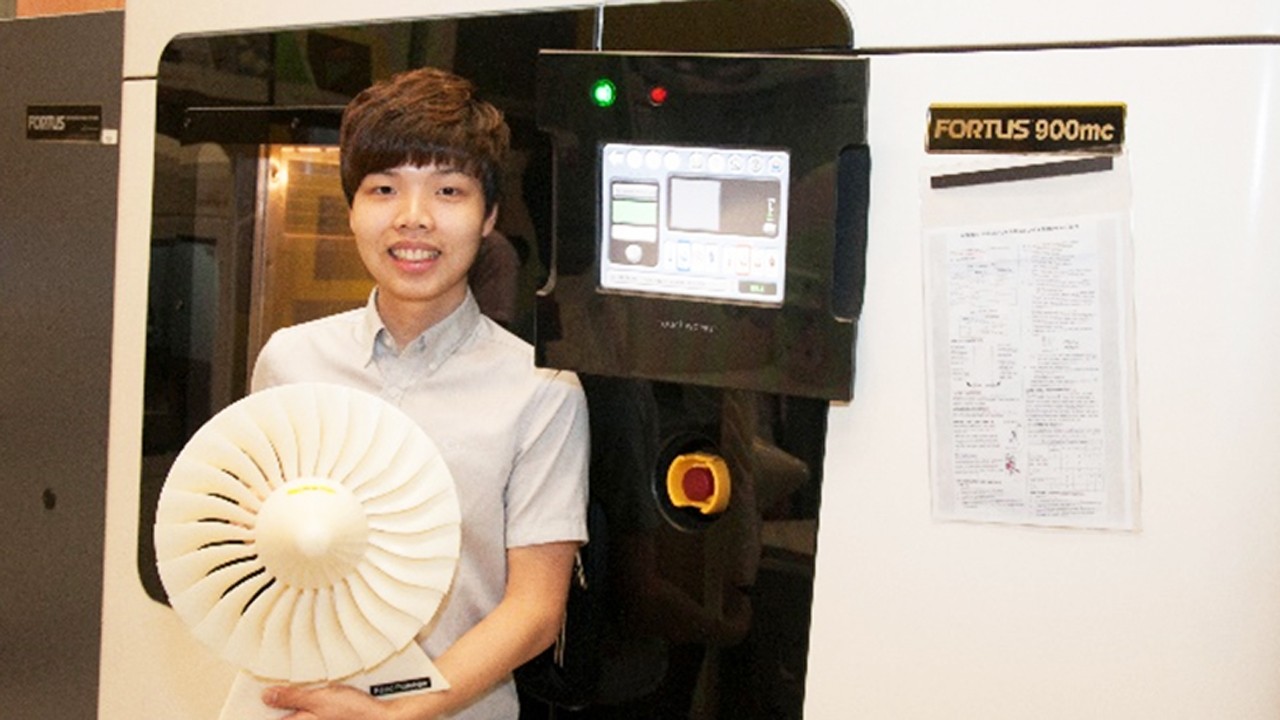
Fused Deposition Modeling (FDM) Processes Stratasys Fortus 900mc
Process:
The extrusion head heats the filament and ‘draw’ section of the part on the build platform. Model is built upwards in layer.
Material Used:
ABS, PC, PC-ABS, Ultem
Maximum Build Size:
900mm x 600mm x 900mm
Application:
- Conceptual model
- Fit, form and functional applications
- Investment casting
- Other applications
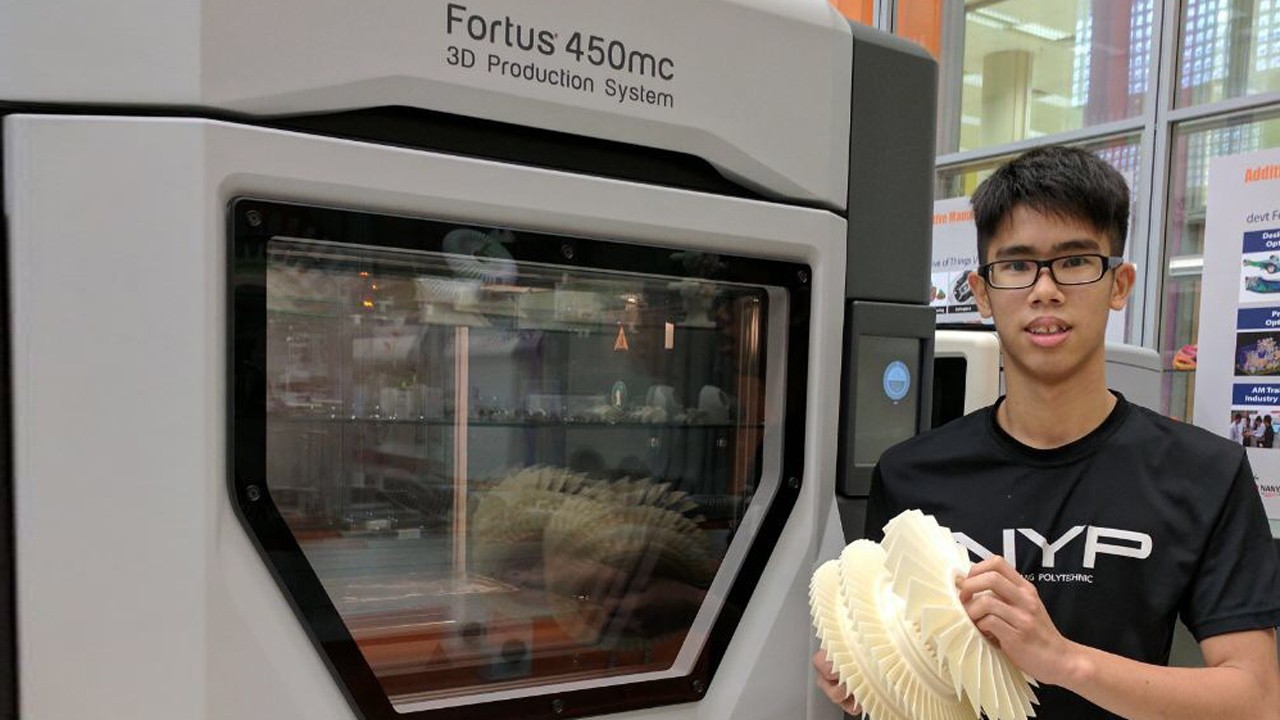
Fused Deposition Modeling (FDM) Process Stratasys Fortus 450mc
Process
The extrusion head heats the filament and ‘draw’ section of the part on the build platform. Model is built upwards in layer.
Material Used:
ABS, PC, PC-ABS, Ultem
Maximum Build Size:
400mm x 350mm x 400mm
Application:
- Conceptual model
- Fit, form and functional applications
- Functional prototypes
- Other applications
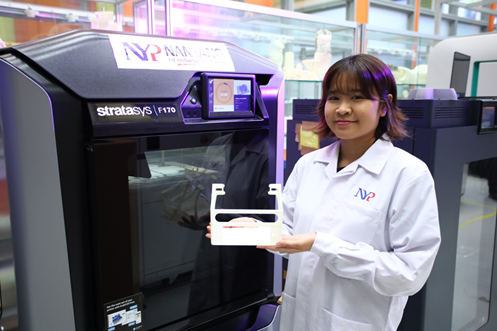
Fused Deposition Modeling (FDM) Process Stratasys Fortus F170
Process:
The extrusion head heats the filament and ‘draw’ section of the part on the build platform. Model is built upwards in layer.
Material Used:
ABS
Maximum Build Size:
254mm X 254mm X 254mm
Application:
- Conceptual model
- Fit, form and functional applications
- Functional prototypes
- Other applications

Fused Deposition Modeling (FDM) Process VSHAPER PRO
Process:
The extrusion head heats the filament and ‘draw’ section of the part on the build platform. Model is built upwards in layer.
Material Used:
PEEK, PLA, ABS
Maximum Build Size:
270mm x 270mm x 200mm
Application:
- Able to fabricate precision parts using PEEK which is highly resistant to heat and chemicals with detailed mechanical features
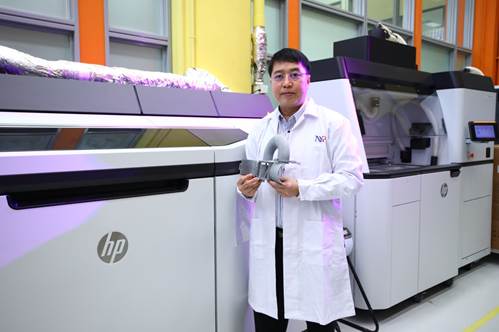
Multi Jet Fusion Process HP Jet Fusion 5200
Process:
Powder-based technology utilising IR energy to fuse powder with light-absorbing ink and detailing agent.
Material Used:
Polyamide (PA 12)
Maximum Build Size:
380mm x 284mm x 380 mm
Application:
- Conceptual model
- Fit, form and functional applications
- Functional prototypes
- Other applications
Other Services
Additive Manufacturing Innovation Centre can be the gateway to other services within NYP. We are able to provide one-stop solution to the industries. We can link our customer to services such as Finite Element Analysis, Mould Flow Analysis, Reverse Engineering and many other services.
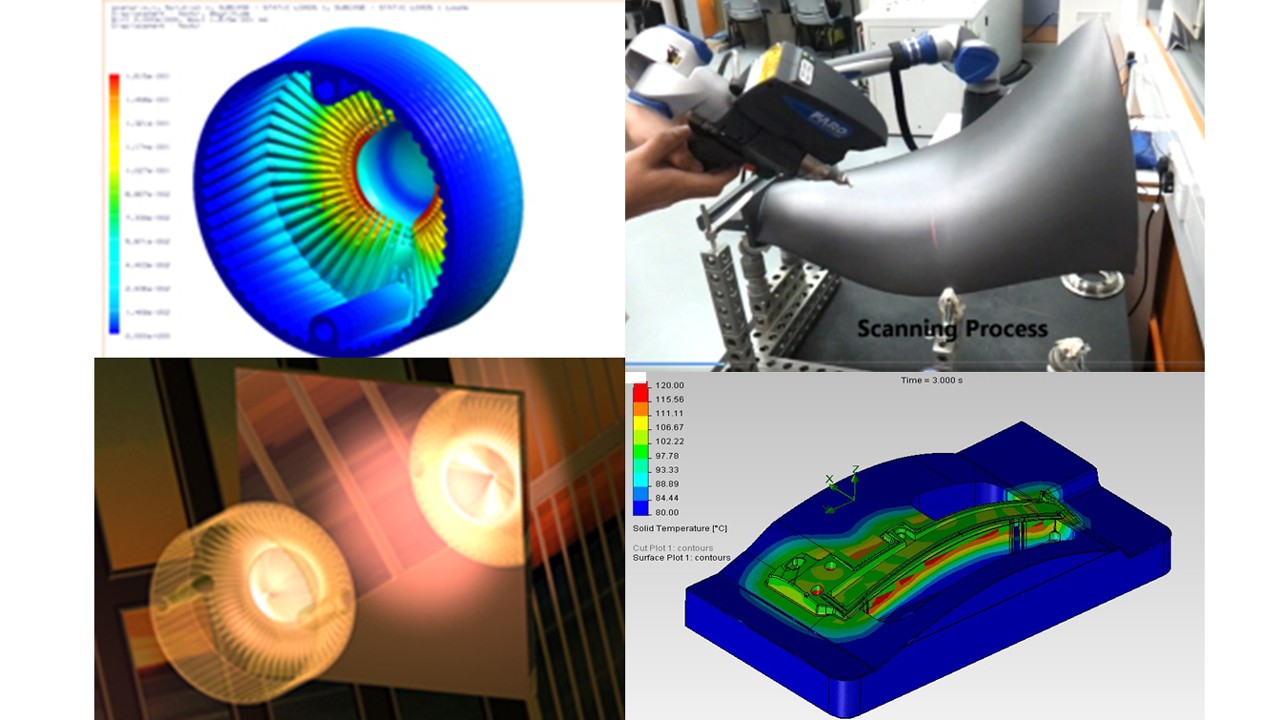
Contact us
Mr Desmond Tan
Centre Director
- Tel: 6550 0674
- Email: desmond_tan@nyp.edu.sg
Mr Zaw Hlwan Moe
Lead Specialist (Additive Manufacturing)
- Tel: 6550 0667
- Email: zaw_hlwan_moe@nyp.edu.sg